Services
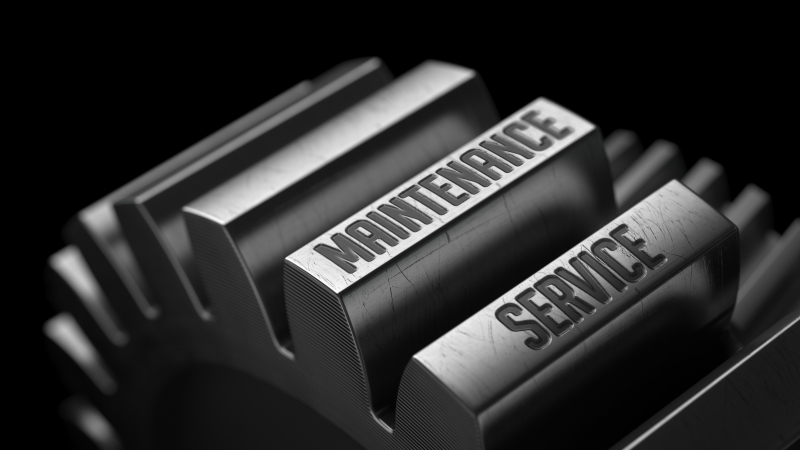
Bogaert Transmission has a team of engineers and technicians that ensures that clients’ production can continue at maximum level. Every maintenance is meticulously prepared. The aim is to work as efficiently as possible during the maintenance days planned at the plants.
The Services team thanks its expertise not just to years of experience. By investing in regular training and exchanging know-how, they keep lifting the department to a higher level. Feedback from manufacturers and producers is also always taken to heart.
Bogaert Transmission combines expertise with a proactive, sound approach. It is precisely this combination that its clients appreciate.
Inspection & analysis of product lines
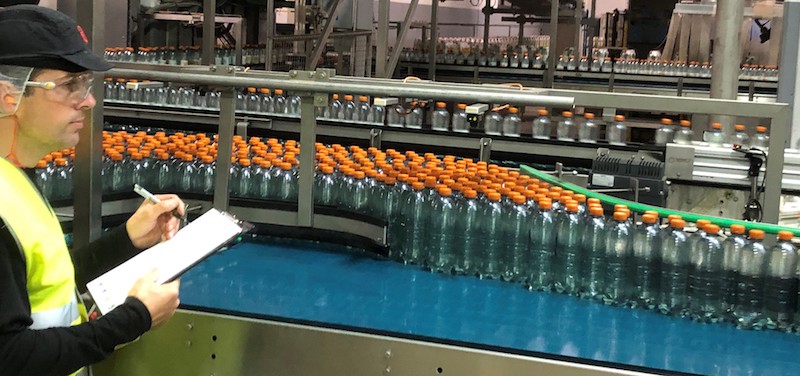
Thanks to regular inspections of product lines, Bogaert Transmission can clearly report which repairs or replacements are required. An inspection report charts the issues and sketches a detailed plan of approach as well as the accompanying price tag. It contains an analysis of the parts that need replacing or repairing. This has nothing but advantages for the clients: better control of the budget, limited downtime of the production line and the certainty that there will be no unexpected failure of the machines.
You can find an example of an inspection report here:
From analysis of the needs to the choice of product
After an inspection by Bogaert Transmission, you know precisely what product is almost worn through and needs replacing. Since the range of products continues to develop and expand, it is often not obvious for our clients which replacement product to choose. Is it best to choose the same equipment or for something with a longer useful life? Of perhaps flatter equipment with less product emission? Other possibilities include the same equipment but with simpler assembly and disassembly, standardisation throughout the company, a maintenance-free version or dry-running chains or … Luckily, Bogaert Transmission can help you look for the best quality and version geared to your production needs.
Thanks to our years of experience and the combination of the measurement, analysis, delivery and on-site replacement of these components, the Bogaert Transmission experts can offer you the perfect solution. This makes Bogaert Transmission the reliable partner of your company.Customised in our own workshop
Bogaert Transmission’s workshop definitely offers each client added value. Often, parts have to be adapted to the specific production needs of the client. There isn’t a single part that cannot be adapted by the Bogaert Transmission team. It analyses each request and finishes the equipment needed within the timeframe provided. The transmission parts are finished and produced in our own workshop. In this way, clients’ production is never threatened.
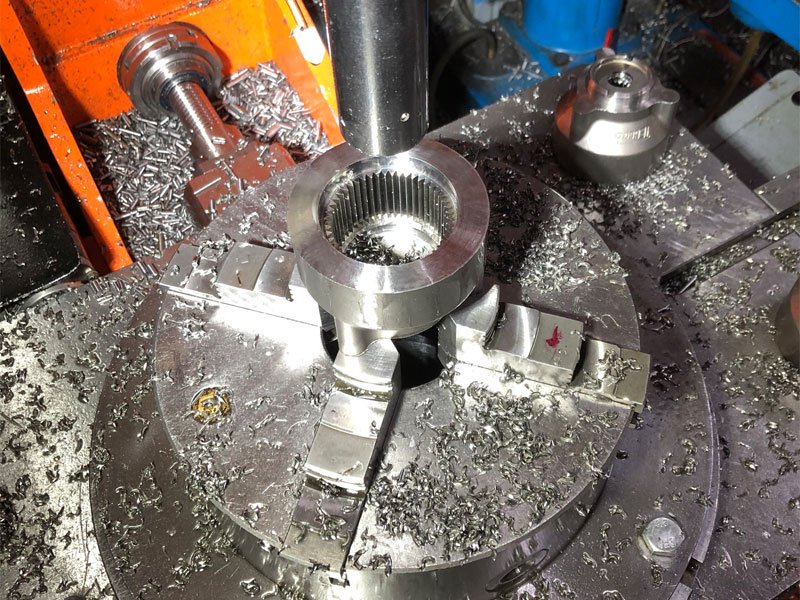
On-site assembly and maintenance
Bogaert Transmission has a team of experienced technicians that assembles the products ordered by the clients on site. It installs the chain and belts of conveyors but also all the other parts in the Bogaert Transmission range. At the client’s request, this is often accompanied by the periodical maintenance or inspection of the production lines. Whatever the assignment, the team guarantees quality and always boosts client satisfaction.
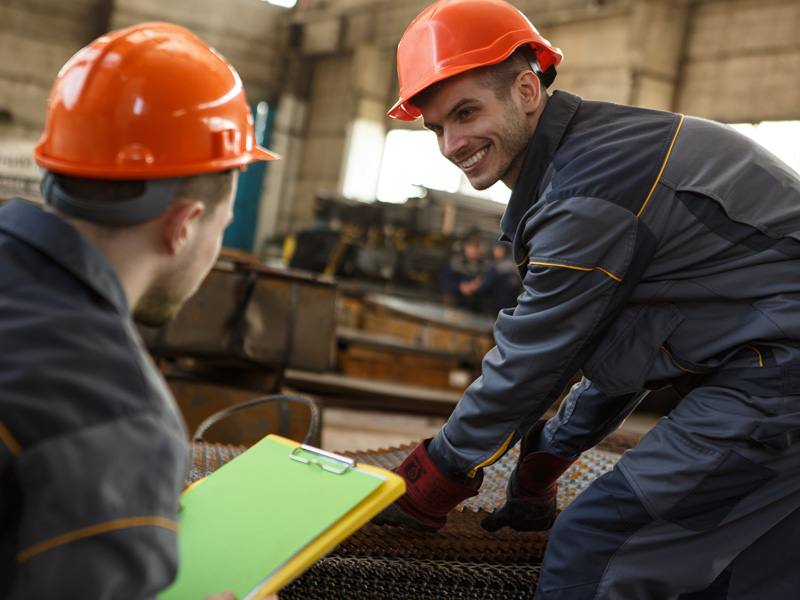
A few satisfied clients
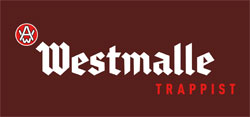
The abbey of Westmalle is famous for its Trappist beers that is drunk far beyond Belgium’s borders. Bogaert Transmission ensures that the bottling line always runs at its best. Once a year, it schedules the maintenance of the machines and conveyor belts. The conveyor engineers of Bogaert Transmission carry out an analysis in advance. This means that they can work quickly and efficiently during the maintenance week. The team also clearly charts what parts of the crate and bottle conveyors have to be replaced. In this way, Bogaert Transmission anticipates any possible production downtimes and/or production losses and schedules the necessary repairs.
“It is a pleasure to work with them. Communication is smooth, they react quickly and even take care of delivering and replacing parts where necessary. In short, a partner with the right know-how and a very sound approach.”
“For Abdij der Trappisten in Westmalle, working with Bogaert Transmission can be summarised in just one word, and that is “reliable”. Thanks to the smooth maintenance of the crate and bottle conveyors, the production of the brewery can run at full all year long. An absolute win for the abbey and its customers!’’ Johan Peeters, maintenance manager at Brouwerij der Trappisten in Westmalle”
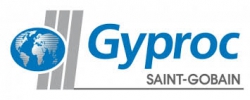
Gyproc Saint-Gobain delivers plasterboard and all the accompanying materials to over XXX points of sale throughout Belgium and the Netherlands. For almost ten years, the company has worked with Bogaert Transmission for the delivery of parts such as MatTop belts. “Bogaert Transmission sees the whole picture: reliable price offers, the right know-how and clear communication. It is a joy to work with them. In the spring of 2019 their conveyor engineers team carried out an extensive inspection of our conveyor belts. The result was a detailed report that charted the wear and tear. We could order the parts or FlatTop chains that were worn from Bogaert Transmission or replace them ourselves. From now on, we are scheduling a yearly inspection. Bogaert Transmission’s professional report makes it possible for us to respond quickly. That guarantees our production. And that continuity is essential for our company and our customers.”
“You can count on Bogaert Transmission for a regular inspection of the conveyor belts. This spring their conveyor engineers carried out a detailed inspection of our belts. The wear and tear was carefully charted. On the basis of that professional final report, we were able to schedule the necessary action. Bogaert Transmission looks at the whole picture: reliable price offers, the right know-how and clear communication. It’s a joy to work with them.”